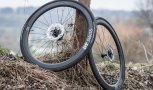
Testing to perfection: the Syntace method
Syntace give you the absolute assurance that their components will last. Surprisingly, that doesn’t mean heavy.
Syntace products have something special: the absolute assurance that the components on your bike will last. Surprisingly, that doesn’t mean heavy because Syntace parts are some of the lightest on the market. How is this possible? It became clear to us when we visited the Syntace Headquarters in Tacherting and were allowed to look over the shoulders of their testing experts.
A well-known dilemma...
Most of us simply want to have fun riding our bikes and not have to worry about the components failing us. However, we are faced with a common dilemma, for a part to be durable, it usually has to be heavier. On the other hand, you can have more fun when the bike is lighter. The only way to achieve both, durability and weight optimization, is to put time and energy into the careful development of products, and Syntace does just that. For example, a stem like the Syntace Megaforce 2 isn’t developed overnight. Much time is spent designing the product even before it reaches final computer mockup and even more time is spent putting the product through various tests.
And Syntace has plenty of machines. For almost every component they have developed, there is a proprietary machine for it.
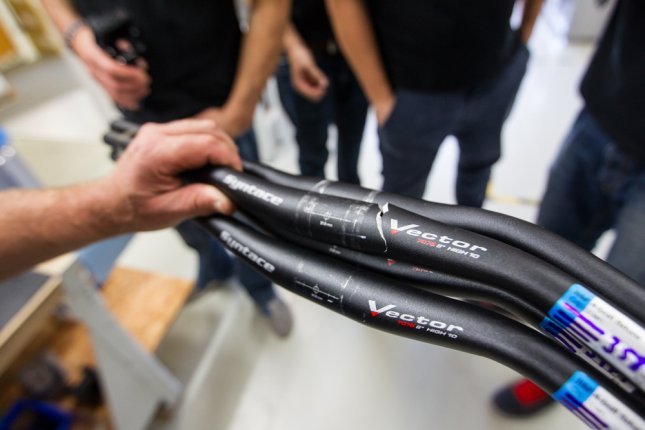
Broken handlebars from a sample group. These are kept for 10 years.
The testing workshop is of such high quality that countless magazines rent out the space for comparison tests. Even other manufactures use the space to test new prototypes. In my opinion, this demonstrates the quality of the testing machines. One could say, for example, that the handlebar testing machine, VR-3, set a new industry standard.
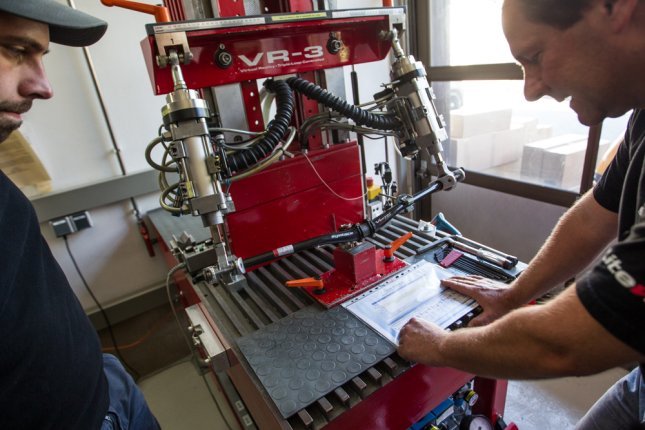
VR-3 Handlebar Testing Machine
How does Syntace develop safe and lightweight components through testing? It is possible because each prototype is tested on a machine made specifically for that purpose. Resulting from many years of experience, Syntace has a large data pool that allows them to pull all the information from previous tests. Analyzing this data allows them to predict, for example, at what load and where a set of handlebars will break.
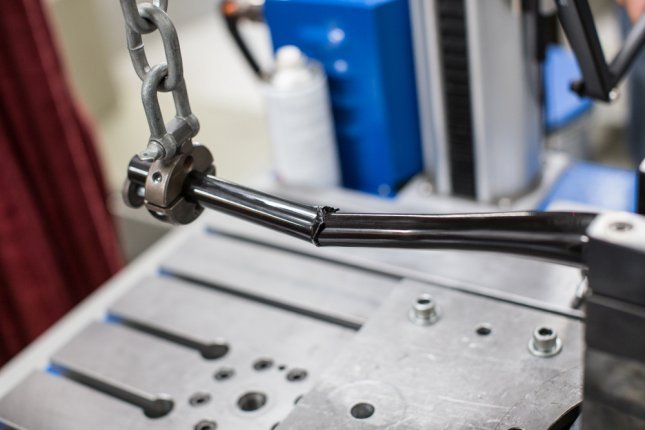
In quality control and development, the handlebars are tested to breaking point.
One recognizes quickly that maybe another layer of carbon fiber is need on a certain section. Or do the handlebars break in a completely different place? Was the ability of the material stretched too far? To answer these questions is easy: try, fail, repeat. The products are tested until the they are as good as the previous model. The tests not only find weak points, but they also can tell where the overbuilt points of the product are allowing those areas to be pared down to reduce weight. Even though the testing procedure is extensive, nothing can replace the true test riders riding their prototypes.
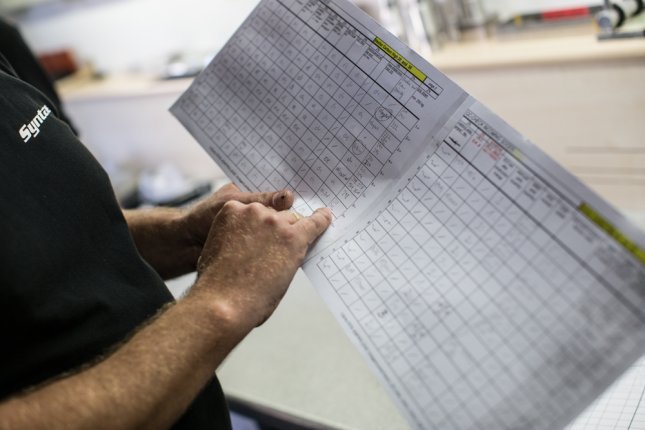
Sample group documentation from a shipped batch.
Every new idea and innovation is tested to its extremes. No product is released if there is a shred of doubt about its safety and functionality.
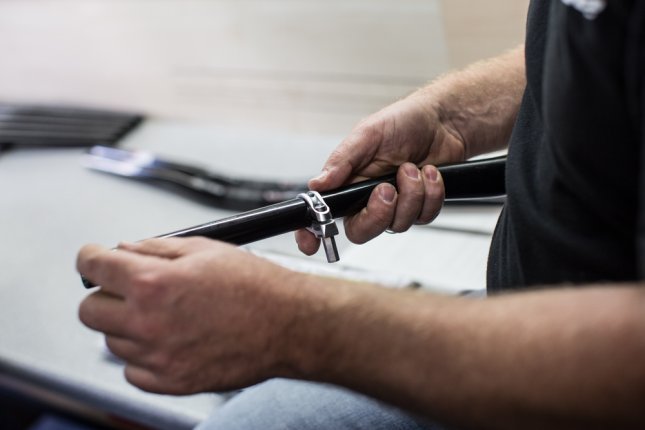
Clamp Test
One of the first tests is the clamp test. A clamp is mounted on 3 different points on the handlebars to the required Nm. The sharp edges of the clamp will dig into the carbon bars damaging the material. If the handlebars were incorrectly manufactured, the weak points could easily be identified when they bend or break.
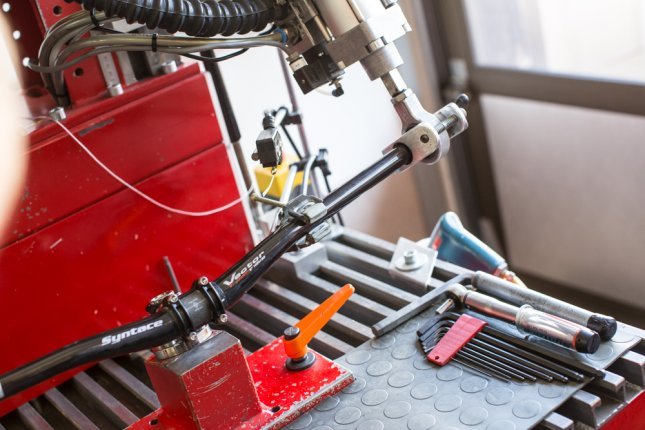
Handlebar testing machine: simulating standup pedaling, runs, and jumps.
Onwards to the VR-3. The handlebars are mounted on a stem just like on a bike. The stem is fixed to the machine. Hydraulic cylinders are then attached to the right and left sides of the bars. This ensures a close-to-reality load. The cylinders can push and pull just as a rider would on a jump or when standup pedaling.
Mounted in this way, the handlebars go through a defined test cycle. The following scenarios are simulated:
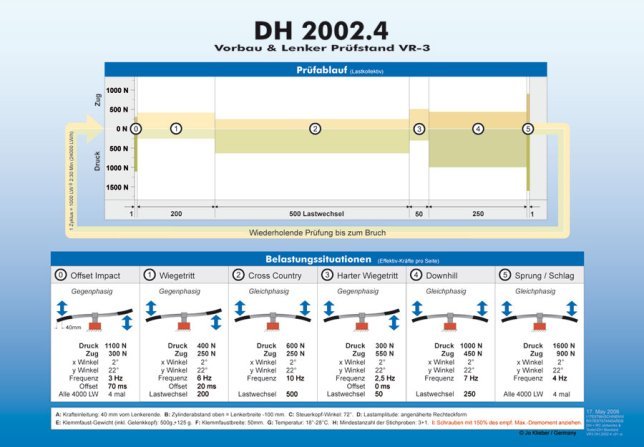
Test Sequence
Everyday riding situations like standup pedaling and Cross Country like loads are tested, but Downhill and jumps are sprinkled in as well.
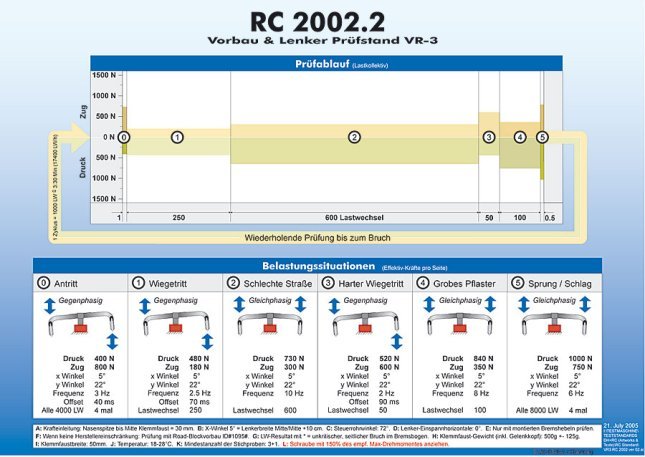
Test Sequence
When standup pedaling is tested, 55 kg is pulled on one side and 30 kg is pressed on the other. All of it at a realistic frequency and repeated 50 times.
When running Downhill tests the left and right side are pulled at a 100 kg then pushed with 45 kg. This is repeated 250 times. Under these types of loads the handlebars should withstand all possible riding conditions.
Sounds pretty impressive. When you then realize that all of that will be repeated for multiple days then it becomes fascinating. Multiple days on this machine is the equivalent of 20 years of riding.
As mentioned above, Syntace tests almost every product they develop. This includes a pedal testing stand that is always spinning and at the same time is applying forces to the pedals.
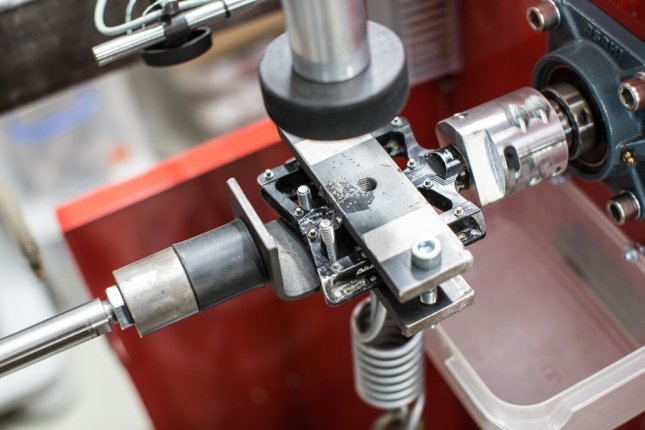
Pedal Testing Stand
Now decisions like bearing changes, grease enhancement, or a new pedal body design can be made.
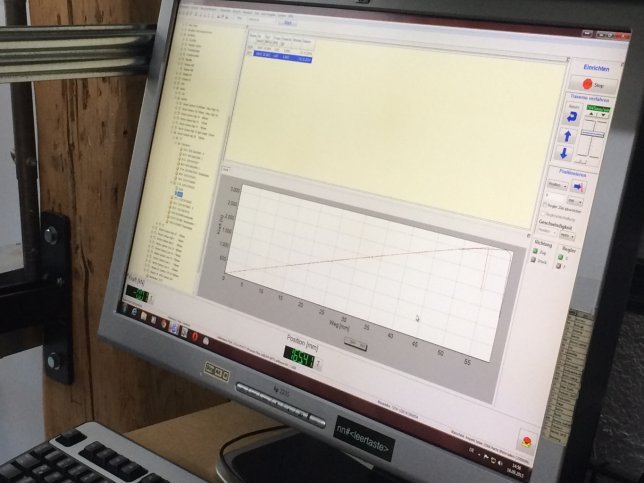
-
The wheels need to be tested as well, so Syntace has a wheel testing stand that is running 24 hours a day testing a new wheel. The wheel is first fixed to the machine like you would fix a wheel to the rear triangle of your bike. Without pause, the machine uses a drum to spin the wheel. The drum has various height differences to simulate riding over roots, or cobblestones.
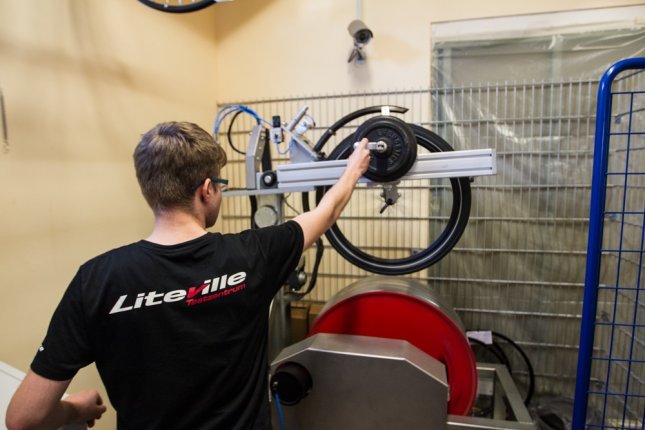
Wheel and Tyre Testing Stand
To make things as realistic as possible the wheel can be tipped to simulate corners. Seeing that was astonishing, but also extremely loud!
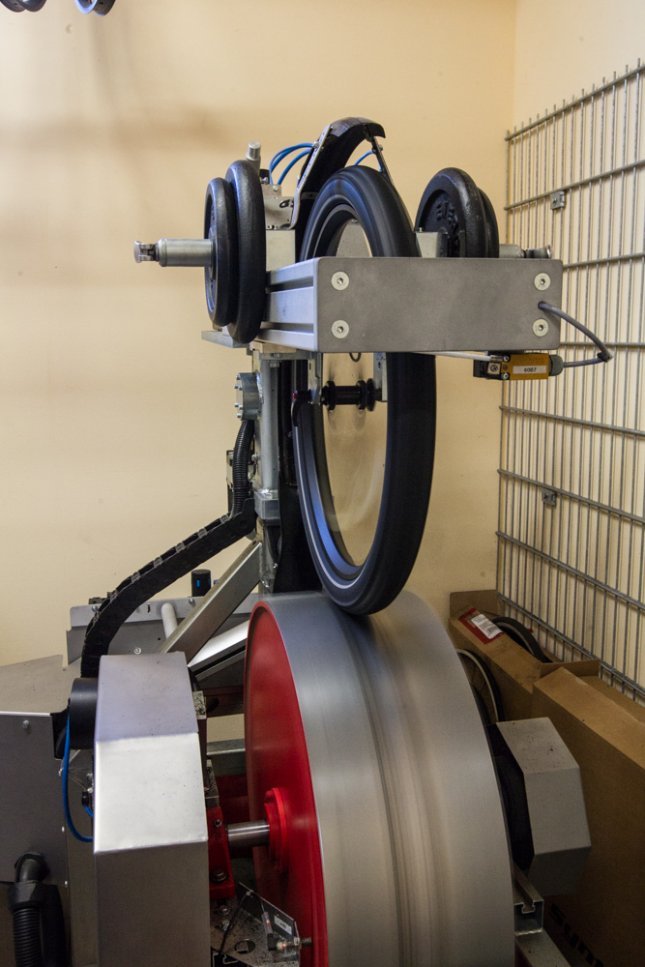
Wheel and Tyre Testing Stand
All these tests don’t just help with development. They help quantify their quality over and over again through repeated tests. From every shipment, one componentis taken and is tested. The “Destroyer‘s” name is well earned as he is the one who pulls the test components to check the quality of each shipment. Even the water bottles are tested: Do they leak? Is the 400 ml mark really where it should be? And not to forget the labels, are they sticky enough? This is German perfectionism.
The above video shows how Syntace takes a certain percentage of seatposts out of a shipment for quality control testing.

Testing stand for seatposts: similar to the handlebar test
If the carbon seatpost breaks at more than 250 kg, then it meets the quality standard. However, on average the seatposts break at 300 kg.
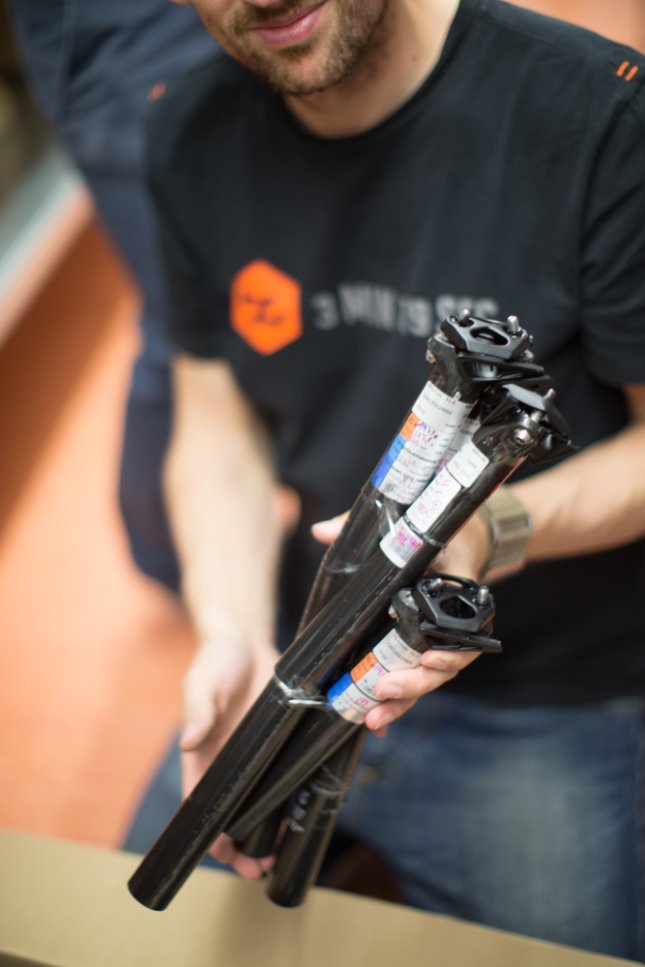
The Archive: Samples of every shipment are kept for 10 years.
After every test the test component is stored with the samples from the batch it belongs to just in case something happen. So far, they have never had to reference them.
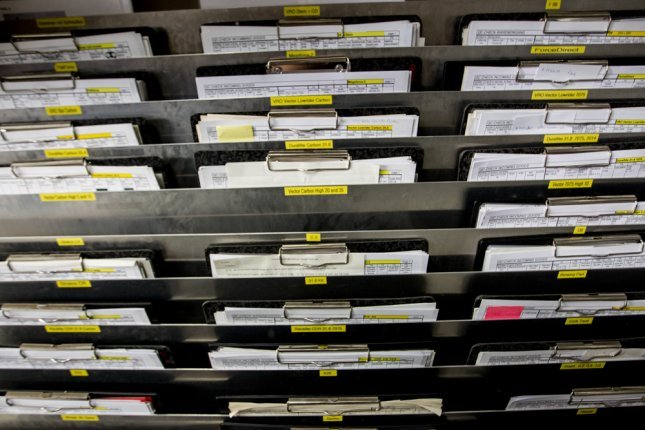
Documentation is everything
On the Syntace terrace, components like stems and handlebars can be found lying in neat rows. Here the long-term effect of the weather on the components is checked.
My personal impression: optically not as pleasing as something new, but they function as if they were manufactured yesterday.
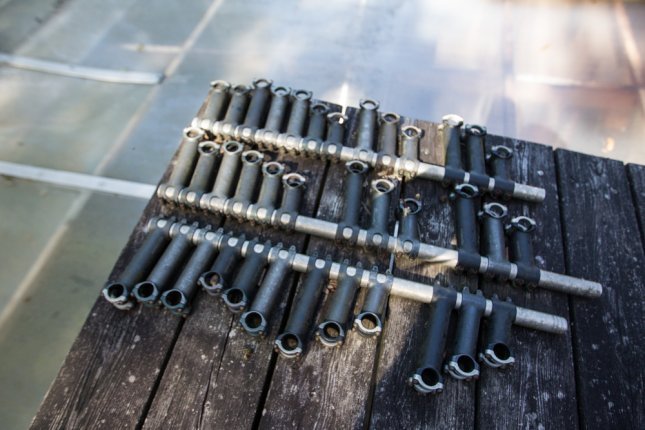
Long-term test on the balcony
For me, this is what makes Syntace stand out from the crowd: Blood, sweat, and probably tears have been thrown into this business. It is “living engineering” and not just computer simulated. Large amounts of effort are put into testing the components as close to reality as possible. Syntace has a thirst for learning and improvement. That’s why they do the tests they do.
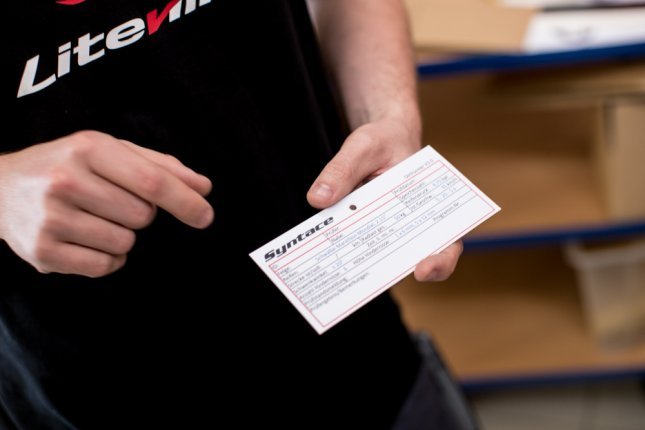
We trust Syntace 100%
If I could say just one thing: I trust my Syntace components without a doubt. Hats off to their quality standards!