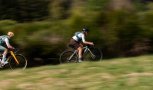
Hope Factory Visit in Barnoldswick, England
Visiting Hope’s factory was a dream come true. Finally, a chance to see where the precise components come from.
Since I started mountain biking, the brand Hope has always peaked my interest because they are known for high quality manufacturing. That’s why I was so excited to get a chance to personally check out their factory in Barnoldswick, England.
First impressions
As soon as we parked, the sleek Hope logo caught my eye. Robin, our guide for the day, came out to greet us, using his perfect German. In the lobby we were surrounded by some of the most beautiful Hope parts every made and Robin began to tell us about the company’s history. Hope started out making MTB and motor bike parts, and eventually stuck to MTB components. It was especially interesting to see some of the original bicycles ridden by Hope athletes that were also in the lobby.
Where the magic happens
After leaving the lobby, we were taken to one of the workshops where the fist HB160 carbon MTB’s were on display. Moving on, through doors with crankarms as handles, we had a look at their office where everything from Marketing to Accounting is located.
They showed us where their lights are produced and where the employees take a nice break during the day. After, we were brought into the most exciting part of the tour. The room filled with all of the CNC machines and laser engravers that have made Hope famous. It was great to see the raw metal next to every machine, knowing that each piece is turned into one of Hope’s precise components. It was easy to tell that everyone working here truly loved their job.
When we were done drooling over the machining, we were allowed a quick look into Hope’s carbon production where handlebars and frame are developed and put to the test. Afterwards, we hit up the anodizing section of the factory. Here, is where all of Hope’s signature colours come alive.
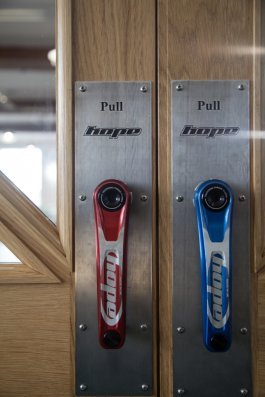
Hope cranks open doors.
As a final treat, we were shown the quality control part of the manufacturing process. It was easy to tell that each product is extensively tested and brought to its limits to make sure everything is a durable as possible.
The day ended with sandwiches and chips in the break room. We had an unbelievable time and a big shout out to Hope for their hospitality and amazing products!