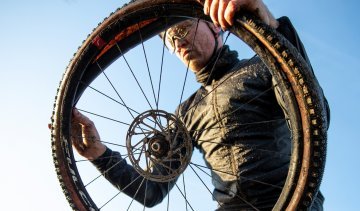
Bicycle inner tubes for road bikes or MTBs: Wha...
Bicycle tube or tubeless tyre? Butyl, TPU or latex? Find out which system is best for you and your bike here.
The question: system wheelset or build your own wheel? We explain the basics for picking out rims, spokes and hubs.
Overall, a consists of a hub, a number spokes with spoke nipples and a rim. Everything else, such as the freehub, cassette, axle, brake discs or tyres, will be covered in other articles. How carefully these components are selected and combined with each other determines the service life of the wheel. These days, there are a lot of good ready-made wheels or system wheels to buy, which is why not every shop always builds their own wheels themselves any more. System wheels are available in light, stiff, robust or budget models. However, they are often characterised by the use of manufacturer-specific components. Therefore, one is dependent on the specific component in the event of a defect. This is where a wheel needs to suit the needs of a wider range of people. When you build your own custom wheel, you can tailor it to suit your needs, but it does require a greater amount of effort.
When bearing loads, namely when riding your bike, that’s when the wheel gets to work. The weight of the rider and the bike rests on the hub, which in turn rests on the upper part of the rim. The lower spokes are "relaxed," which means the wheel therefore works permanently. You can't see it with the naked eye, and you can't hear it either. What is immediately obvious is that there are wheels with different numbers of spokes. The most common spoke counts are 24, 28, 32 and 36. Nowadays, apart from system wheels, a spoke count of 32 the most common. The quantity does not necessarily say anything about stability and weight, but it can be an indication. The number is always divisible by four, because there are inner and outer spokes on both sides of the hub – making four types. Furthermore, it is important that the number of spoke holes on the hub and rim match. On mountain bikes, spokes are almost always triple-crossed, meaning that each spoke crosses three opposing spokes between the hub and the rim. This gives the rider the optimum balance of stability and elasticity. Other patterns such as double-crosses are possible, which we will go into more detail elsewhere.
When it comes to hubs and spokes, the bicycle industry is almost unanimous: hub bodies are made of aluminium and spokes are made of steel. There are also spokes made of aluminium, titanium, carbon or textile fibres, or hubs with carbon parts; however, they have a relatively small presence on the market overall. Rims, on the other hand, were often made of steel in the past, but are now mostly made from aluminium and more and more often from carbon. Aluminium rims are cheaper, and carbon rims can be precision-crafted to conform to the desired level of stiffness or flexibility. Aluminium can also be anodised in a variety of colours, allowing for even more wheel customisation.
The spoke is a wire made of steel; its number and pretension result in the wheel’s stability. Traditional spokes are J-bend spokes, and feature a curved end with a flat spoke head that is threaded through a hole in hub flange. The other end of the spoke is threaded onto the part where the nipple is screwed. The spoke is effectively a bolt, and the nipple is a nut. Hubs without a classic flange require what’s called straight pull spokes, which bear an even greater resemblance to a bolt because they have no bend and are threaded straight into the hub's spoke seat. Truing straight pull spokes is more difficult because you have to keep them from spinning.
The differences in quality, price and weight of the spokes are found in their shape and thickness. Usually, bicycle spokes are 2 millimetres thick at the head and thread. Smooth spokes are spokes that have the same thickness throughout (e.g. DT Swiss Champion or Sapim Leader. With so-called thickened spokes (e.g. DT Swiss Alpine III), the spoke arc is reinforced. Sport wheels typically use so-called double-thickness spokes, which are slimmer in the longer straight part, such as DT Swiss Competition and Sapim Race (both 2.0-1.8-2.0 mm) or DT Swiss Revolution (2.0-1.5-2.0 mm) spokes. While the spokes mentioned so far feature a round cross-section, there are also bladed spokes with an oval cross-section (e.g. Sapim CX-Ray). They have better aerodynamics from 35/40 km/h and are a little more durable thanks to machining processes.
The nipple has an inside thread and is screwed onto the spoke. It is inserted from the outside through the rim onto the spoke, and screwed with the head against the rim base. To make installation easier, most nipples have a slot in the head, and some nipple heads are hexagonal or are shaped like a hex key, also called a torx tool. The square sleeve nut that you attach the spoke wrench to has a standard dimension of 3.23 millimetres – older wheels may have other dimensions. A suitable nipple tensioner, also called a spoke wrench, prevents unnecessary wear on the nipple.
Nipples are available in brass and aluminium. While alloy nipples are two-thirds lighter than brass nipples, the latter are more resistant to corrosion, so are recommended for all-season city bikes or winter training equipment. There are also nipples in different lengths, with the most common being 12-millimetre nipples. Longer nipples (14 mm, 16 mm) theoretically provide more threads to hold or compensate for shorter spokes. Some rims have a very strong rim base, while others require shims, such as Newmen rims. Even then, longer nipples are generally advisable.
The hub sits in the centre of the wheel, holds the spoke heads, and does the actual turning work. In conventional hubs, the spokes sit in the hub flanges, which are the two plate-shaped highest points. In straight pull systems, the flange does not form a plate and has a significantly smaller diameter. The two flanges of a hub can have the same or different diameters. The space between the flanges determines (besides the rim diameter ERD, see below) the spoke angle. The flatter the spoke angle, the more stable the wheel, which is why hubs have become wider in recent years. Front wheel hubs for rim brakes are symmetrical; with disc brake hubs the brake disc needs space on the left side, which is why the left flange is indented. Rear hubs are much more often asymmetrical because they have to make room for the cassette on the drive side. Symmetrical rear hubs are found on singlespeed or track bikes. As a result of all this, you will most likely need spokes of various lengths on the left and right side of the rear wheel, so that the rim rests centrally in the frame at the end. However, the difference can be reduced or compensated by asymmetrical rims or unequal hub flanges. On the front wheel, the deviation may be so slight that the same spokes will fit on both sides. When you measure the hubs yourself, you determine these values: over locknut dimension, flange distance, flange centre to the outer edge left and right (or to the centre, depending on the calculator), flange diameter and spoke hole diameter.
The rim holds the spoke nipples on the inside and the tyre on the outside. Rims for rim brakes have a brake flank and wear out over time, while rims for disc brakes can be designed without this feature, which makes them lighter and theoretically extends their service life. Under no circumstances should you combine disc brake rims with rim brakes! In the past, rims were U-shaped, i.e. they consisted of only one wall; they were also called box rims. In order to achieve more rim stability, especially when aluminium became the material of choice, so-called double wall rims were constructed, which were given a second rim base. This is still the prevailing design today, even for carbon rims. An interesting recent exception is the 3Zero Moto from Zipp, which is constructed from carbon but sporting the old box shape, allowing it to intentionally flex without breaking. Most rims are symmetrical, but there are also those with asymmetrical profiles to help compensate for corresponding hub assymetry.
The spoke holes in many rims have either a right or left orientation.
The ERD indicates the effective rim diameter down to the millimetre. This is important when determining the appropriate spoke lengths for a given wheel. 26 or 28 inches would be far too inaccurate there. Strictly speaking, the ERD is the maximum distance of the rim base, i.e. the two points where two exactly opposite spokes rest with the nipples on the rim. However, ERD is measured differently. The manufacturers NoTubes and Mavic for example measure the rim base. DT Swiss and others already add 3 millimetres to the ERD of their rims so that the spokes utilise the nipple thread as much as possible. Spokes with the perfect length extend to the slot of the nipple on the finished wheel. To measure the ERD of a rim yourself, it is best to use two old spokes with the nipples turned up, the heads cut off and markings to make the measurement easier. Always measure several places to determine discrepancies!
To figure out the correct spoke length, you can turn to one of the many spoke calculators on the internet. The advantage of using calculators from large manufacturers is that they are based on reliable databases which store information on commonly-used rims and hubs. However, it won’t hurt if you measure components yourself and cross-reference data in the database. You’ll need the ERD of the rim, the dimensions of the hub (see there) and the number of spoke crossings.
The most important tool for wheel building is the truing stand. All models can be used for different wheel diameters, rim widths and axle dimensions. There's a wide price range between basic, single-sided versions like the Pro Truing Stand 2.0 from Feedbacksports and professional-grade equipment like the Truing Stand from DT Swiss. The model TS-2.2P from Parktool has a host of various accessories, from thru-axles to dial gauges TS-2Di, which you won't want to go without once you've used them.
Models that don't align themselves need to be calibrated every so often with a truing gauge like Park Tool's 1554-1. Alternatively, you can check the alignment of the wheel with a wheel truing gauge.
To tighten the nipples, you need nipple tensioners that fit properly – usually the 3.25 millimetre spoke wrench will fit modern nipples. Examples include the red Spokey and the Universal Key from DT Swiss. In the case of bladed spokes, it is recommended to use a spoke holder (e.g. Sapim's spoke wrench for CX/CX-Ray). System wheels from Mavic or Fulcrum require their own spoke wrenches for servicing. Other special tools help to insert the nipple securely into the rim and make the first turns easier. To perfect your wheel, it is also advisable to use a spoke tensioner (Parktool TM-1 or DT Swiss Tensio 2), which allows you to easily determine the tension of the spokes.