
With completely new rubber compounds developed in Germany, Specialized is launching its proven MTB tire models, the Eliminator and Butcher, into the season. The declared goal was to develop compounds that combine balanced damping and excellent grip. You benefit from the feeling of controlling the trail. The result of the meticulous search for the perfect rubber compounds for mountain biking are the compounds T5, T7, and T9, while T2 is reserved for road bike tires. The T in the name stands for "Tread Compound," meaning the rubber compound of the tread. The number indicates the degree of hardness and thus the level of damping and grip.
MTB Tyres
T7
T7 is the all-round rubber compound for trail use, offering a balanced ratio of rolling resistance and grip. It provides comfortable inherent damping that filters high-frequency vibrations, allowing for a smooth ride while keeping rolling resistance and wear at a moderate level.
T9
T9 is the super-grippy gravity compound that offers exceptionally strong grip and traction, bringing the best possible damping so that the tire literally sticks to the ground. Optimal for enduro and downhill riders who are looking for maximum grip. Naturally, rolling resistance and wear are somewhat higher here.
T5
T5 is the rubber compound for cross-country use that particularly focuses on low rolling resistance and durability. Factors like grip and traction are still not compromised, as even XC and marathon riders like to lean hard into the curves. However, the focus is more on speed, agility, and puncture protection.
Gravel Tyres
Road Tyres
T2
T2 is the rubber compound for the center tread of road bike tires, meaning the part that's usually in contact with the ground. Being the hardest of the Specialized mixtures, it ensures that you ride with as little rolling resistance and wear as possible, so you benefit from a fast and durable tire. Meanwhile, the shoulder uses the T5 rubber compound known from Mountainbike Cross Country to enable high cornering speeds and give you confidence on serpentine descents.
More about Specialized

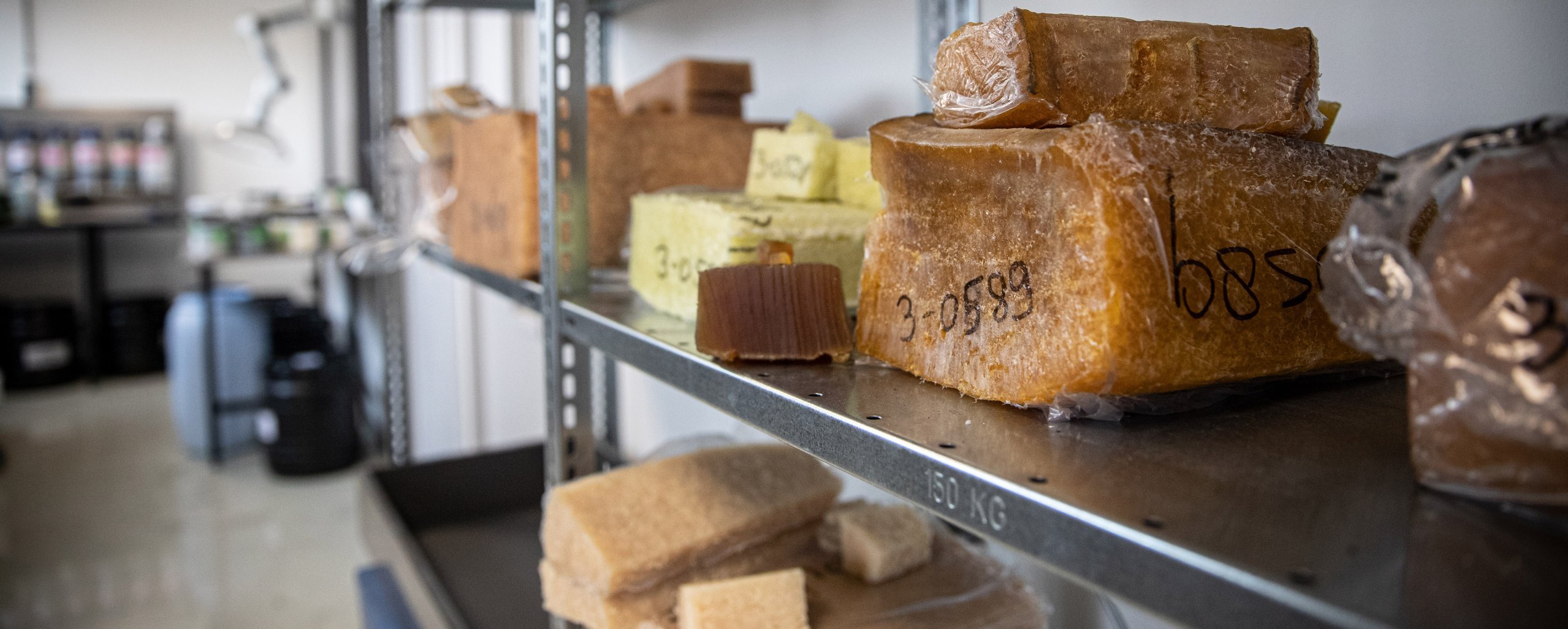
Specialized Test Laboratory for Bicycle Tyres
The tyre jumped off the rim with a surprisingly powerful "rumble," splashing water with enormous force against the glass through which we observed the burst pressure test. That is to say, we should have seen this, but of course we did not witness this crucial moment. In said moment, the building water pressure in the tube blows the tyre completely off the rim, and indicates how much pressure can be applied to the tyre before this happens. Oliver repeats the test for the camera, but the second attempt is far from spectacular, since this time the tube doesn't burst but is rather pushed out like a thick sausage.
Oliver Kiesel and Wolf vom Walde lead a team of five in the Specialized Tire Lab in Bielefeld, Germany. Over the past years they have gradually built out the test laboratory, which stands adjacent to their offices. They can now not only determine the burst pressure, but also measure the tyres’ rolling resistance and perform various tear and puncture tests.
Tread, Carcass, Rubber Compound: In-House Development at Specialized
The past years have led Oliver and Wolf to further develop and refine their in-depth knowledge of bicycle tyres. Together they share many years of experience in the bicycle industry, and their enthusiasm for working with tyres is clearly noticeable. Oliver is responsible for racing and gravel tyres, while MTB tyres are Wolf's speciality. From the development and sketching of various profiles, to the construction of the carcass and composition of the right rubber compounds, everything is in their hands.
"Tread development is certainly the most complex issue," says Wolf as he leads us through the rooms, as we come to a stop before a shelf filled with all kinds of samples and 3D printings of Specialized tyre treads. "But here we are, very far along on the basis of our experience, having broadly expanded our range of profiles for various applications with very satisfactory results."
Everything else, such as the optimal construction of the carcass and the composition of the best rubber compounds, is based above all on trial and error, experimentation and testing.
The Holy Grail of Rubber Compounds
The search for the perfect rubber compound has further driven the duo over the past five years. "We used to have one rubber compound for all our tyres, the GRIPTON® compound. However, we received feedback from our professional drivers that the tyre loses some grip in wet weather conditions", Wolf explains. This issue piqued their curiosity, and thus initiated a meticulous search into explaining “why” this happens “how” to address the problem. They found the perfect partner to join their quest for the holy grail of rubber compounds: QEW Engineered Rubber, a mid-sized compound manufacturer from the Netherlands, with an infectious enthusiasm and downright passion for flexible materials made of long-chain polymers. "We are star chefs here", says Peter Stello, Managing Director and owner of QEW, as he welcomed us during our visit to Hoogezand, Netherlands. This intriguing statement stays with us throughout the entire tour, coming together at the end as we watch machines knead the individual ingredients into a solid mass. Such a sight will never allow us to forget that good pasta and good rubber compounds have much more in common than one would imagine.
Fundamental Research: Of Rubber and Polymers
Around 3,000 compound recipes are stored in the manufacturing database, with more than 500 different ingredients which, depending on their application, prevent buildings from collapsing in earthquakes, ensure aircraft and automotive vehicles maintain optimum ground contact, or which protect tomatoes and peaches from being crushed in transit. Whether it’s doormats, kitchen utensils or rubber seals, the range of applications for the material we simply call “rubber” is nearly infinite, and the knowledge contained in this ever-expanding ingredients list is far from exhausted. Specialized is the first and so far the only partner to work with QEW in the realm of bicycle tyres. "This ensures exclusivity for our tyres," says Wolf with a smile. They have worked together on many recipes over the past five years, trying and testing again and again. "Finding the right compounds for bicycle tyres and their various applications is by no means a trivial issue," says Peter. "You want a lot of grip with relatively little weight on the tyres, but also little rolling resistance and weight in the end product. Without a doubt, the trick here is to search for an optimal compromise." Thus begins the process of stirring up new mixtures, testing and drawing the right conclusions from the data. "We've been conducting some absolutely fundamental research here," says Wolf, looking back on their joint work. They have also worked in cooperation with the Hanover-based German Institute for Rubber Technology, where they have, among other things, carried out "rubber eraser tests", also known as abrasion tests, in order to determine and describe the wear of certain compounds. "All the work was worth it!" claims Wolf. The T5, T7 and T9 compounds address every cyclist’s needs, from cross-country riders demand for speed and good grip even in wet conditions, to downhill riders seeking plenty of grip and shock absorption.
Why are bike tyres always black?
(Or: the parmesan in the pasta)
On average, a rubber compound for bicycle tyres is made up of about 15 different ingredients. With 500 potential ingredients to choose from, the number of possible combinations is seemingly endless. High absorption? Low rolling resistance? Lots of grip? Long mileage? Anything is possible. The only question is: How much of what and when? In the QEW laboratory, various compositions were first mixed together in small quantities and tested to determine their properties. We got a more thorough understanding of this process during the tour:
from the meticulous measuring of individual ingredients, kneading them all together, to measuring the absorption and compression capacity of the finished mixtures. The morning’s experience really showed us how much enthusiasm and care is put into every last detail. Indeed, the machines mixing the solid raw materials are reminiscent of oversized pasta kneaders. Soot is added as one of the final ingredients, which not only gives the rubber its signature black colouring, but also endows it with essential strength and permanent elasticity. The vulcanization process is triggered by heat input ranging from 120° to 180° C. "Think of this like the parmesan on your spaghetti," says Peter. "Without the carbon black that bonds and solidifies the long-chain polymers of natural or synthetic rubber, your tyre wouldn't hold together for 40 kilometres." It also makes the rubber more resilient to environmental ageing caused by UV radiation and various weather conditions.
The Fruits of Their Labour: T5, T7 and T9
Together with QEW, Wolf and Oliver have been perfecting recipes for new compounds for Specialized MTB tyres over the past few years. With great enthusiasm, they show us the damping properties of the three different compounds on various measuring devices, demonstrate the elasticity of the material and describe their influence on the riding feel of the finished tyres. "Our goal was to create compounds that give you the safe feeling of never losing contact with the ground and always having your bike under control on trails," Wolf explains. "The process was a long one, because we had to work meticulously to gain detailed knowledge about the correct composition of the materials and their influence on the tyre’s riding characteristics. Fortunately, we are extremely satisfied with the result!”
However, the new tyres were not only measured and tested in laboratories. Numerous test drivers, from amateurs to professionals, have put the tyres through their paces, providing the lab with feedback and thus advancing development further.
We at bike-components have also tested Butcher and Eliminator MTB tyres with the new T7 and T9 compounds for you in advance. Flo, Chris and Julian all rode with the tyres, and relate their impressions here.