Nicolai ION 16 - Entwicklungsgeschichte eines Rahmens
Ein Mountainbike-Rahmen - entwickelt und gebaut in Deutschland! Wie das geht, habe ich mir am Beispiel des ION 16 bei einem Besuch der Firma Nicolai angesehen.
Ein Rahmen von Nicolai ist für viele ein Synonym für individuelle Bikes und Schweißkunst unter dem Prädikat „Made in Germany“. Doch was steckt wirklich dahinter? Dieser Frage bin ich während eines Firmenbesuchs bei Nicolai auf den Grund gegangen. Hier wurde mir am Beispiel des Modells ION 16 gezeigt, wie ein solcher Rahmen entwickelt und produziert wird.
Der erste Eindruck: Bauerncharme trifft Maschinenbau
Lübbrechtsen.... Wo liegt das gleich? Auf dem Navi wird mir ein kleiner Punkt in der Nähe von Hannover angezeigt. "Klein" trifft es dabei sehr gut. Bereits am Ortseingang ertönt es aus meinem Navi: „Sie haben Ihr Ziel erreicht“. Doch kaum war der Satz ausgesprochen, war ich auf der anderen Seite bereits wieder aus dem Ort rausgefahren. Also, einmal kurz zurücksetzen und schon stehe ich vor dem historischen Bauernhof, der den Firmensitz und die Produktion von Nicolai beherbergt. Und hier sollen all die Rahmen produziert werden?
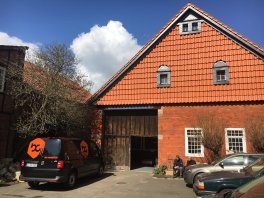
Unternehmenssitz der Firma Nicolai
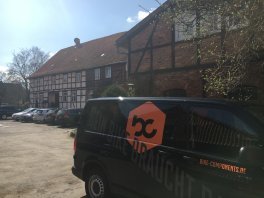
bc T6 vor dem Sitz der Firma Nicolai
Die Entwicklung des ION 16
Bevor ein Nicolai Rahmen entsteht, muss er natürlich entwickelt und konstruiert werden. Hier kommt Marcel ins Spiel, der Entwickler und Kopf hinter dem Modell ION 16. Er hat lange an diesem Projekt getüftelt und erklärt mir im Großraumbüro der Firma die Besonderheiten und Details des Rahmens anhand seiner Konstruktionszeichnungen. Zwar war mir bewusst, dass es nicht einfach ist einen Rahmen zu entwickeln, doch zu sehen, mit welcher Detailverliebtheit Marcel jede Kleinigkeit des Rahmens durchdacht hat, lässt mich einfach nur staunen.
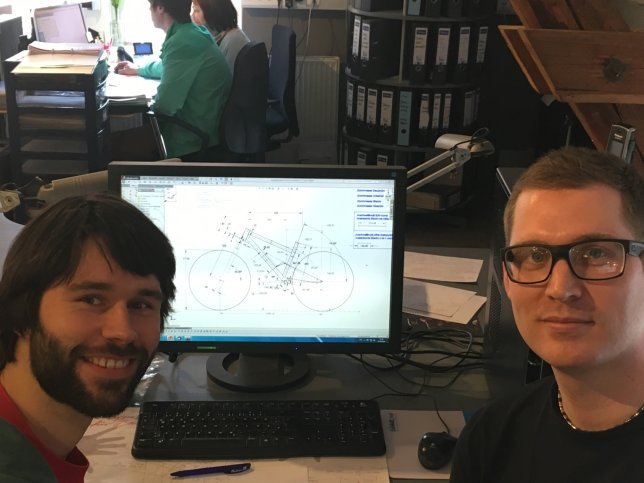
Nicolai Produktmanager Marcel erklärt die Geometrie des ION 16
Neben der Abstimmung der Geometrie auf die Bedürfnisse von modernen Enduro-Piloten, also beste Bergabfahr-Leistungen bei trotzdem guten Klettereigenschaften, wurde auch das Fahrwerk entwickelt, um beste Performance zu ermöglichen. Ein 4-Gelenker sorgt für optimales Ansprechverhalten der 160 mm Federweg am Heck und bietet trotzdem noch Progression, wenn es doch noch härter wird. Darüber hinaus war es für Marcel extrem wichtig eine lange Haltbarkeit des Rahmens zu erreichen. Hierzu spendierte er dem ION 16 breite, 4-fach-gedichtete Lager, welche für einen super geringen Wartungsaufwand sorgen.
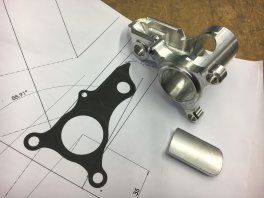
Hauptlager- Innenlager des ION 16
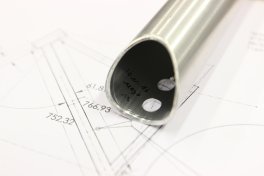
Rohrzuschnitt. Das Loch am Ende unterstützt die Ableitung der Hitze beim Schweißen
Produktion
Mit diesem Hintergrundwissen zum Rahmen geht es nun zur eigentlichen Produktion. Erwartet man von außen noch ein paar angestaubte alte Maschinen, wird man im Inneren der alten Scheune eines Besseren belehrt. Direkt beim Eintreten wird einem der Blick auf große, moderne CNC-Fräsen und Rohrschneide-Maschinen freigegeben. Ein Geruch von Metall, Öl und Maschinen liegt in der Luft und lässt zusammen mit stampfenden und schneidenden Geräuschen mein Herz höherschlagen. Wie ein kleines Kind hüpfe ich zwischen den Fräsen und Maschinen hindurch, um durch die Sichtfenster jeder Anlage zu sehen. Hier werden alle Bauteile eines Nicolai-Rahmens für das Schweißen produziert und vorbereitet. Neben Gussets und Innenlager-Gehäusen werden hier auch die markanten Steuerrohre und Wippen hergestellt. Einfach unbeschreiblich.
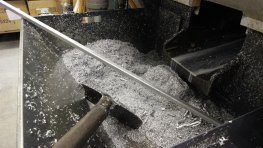
Späne aus der CNC Fräse
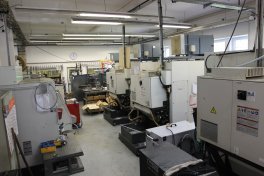
Maschinenpark Nicolai
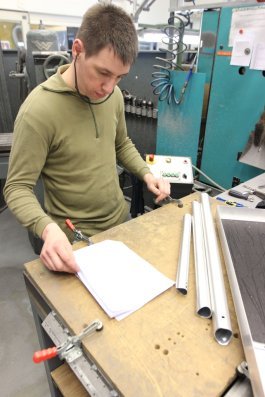
Rohrzuschnitt ION 16 und Gehrung der Rohrenden
Dann folgt der eigentliche Höhepunkt, das Schweißen. Zunächst wird der Rahmen in einer Schweißlehre geheftet, bevor er weiterverarbeitet werden kann. Begleitet von einem hohen und schnellen Surren darf ich dem Chef-Schweißer Sascha zugucken, wie er perfekte Schweißraupen entlang der Dämpferaufnahme des zuvor gehefteten ION 16 Rahmen zaubert. Es ist einfach nur faszinierend, mit welcher Ruhe und Gleichmäßigkeit ein solches Kunstwerk entsteht.
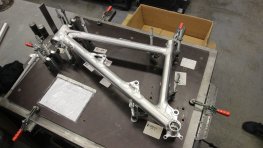
Schweißlehre für den Rahmen Größe "S"
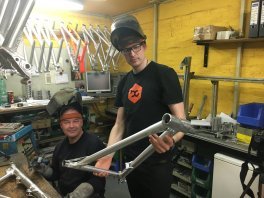
Endabnahme durch Benjamin. 25 Jahre Schweißerfahrung bringt Sascha mit.
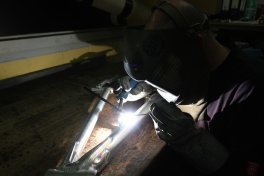
Schutzgasschweißen für die weltberühmte Schweißraupe von Sascha
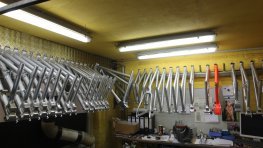
Warteschlange. Hier warten die gepunkteten Rahmen auf das finale Schweißen.
Nach dem Schweißen muss geprüft werden, ob sich der Rahmen durch die Hitze verzogen hat. Hierzu spannt Klaus den Rahmen in eine spezielle Vorrichtung und überprüft mit super feinen Werkzeugen die perfekte Ausrichtung. Bei leichtem Verzug wird der Rahmen per Hand auf Zehntelmillimeter genau gerichtet, bevor er zum Entspannen des Aluminiums in den „Ofen“ kommt. Danach hat sich das Material so sehr gefestigt, dass ein Verziehen des Rahmens nicht mehr möglich ist.
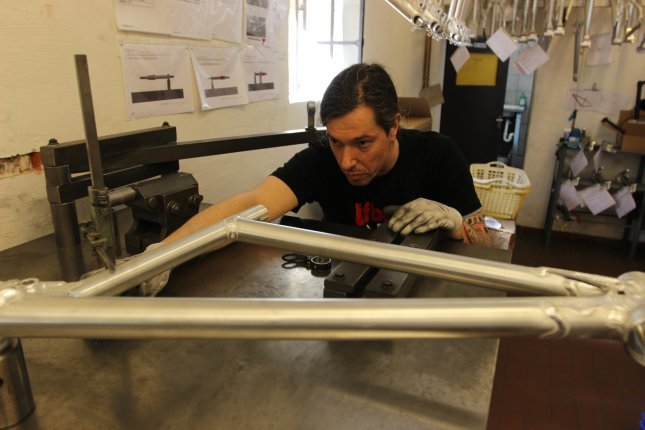
Rahmenrichter Klaus. Bis auf den 10tel mm wird bei Bedarf jeder Rahmen korrigiert.
Während der letzten Arbeitsschritte wird der ION 16 Rahmen nun zur Montage vorbereitet. Neben einer erneuten Qualitätskontrolle werden nun unter anderem die Sitzrohre für einen perfekten Sitz der Sattelstütze ausgerieben.
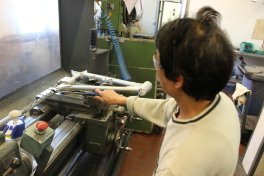
Kai reibt das Sitzrohr für den perfekten Sitz aus.
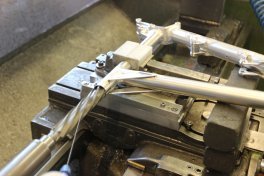
Sitzrohrreibe auf 31,6mm
Ein Rahmen in „raw“ ist nun fast fertig. Aus der hauseigenen „Apotheke“ werden nun alle passenden Anbauteile wie Wippen und Lager genommen, um den Rahmen zu montieren.
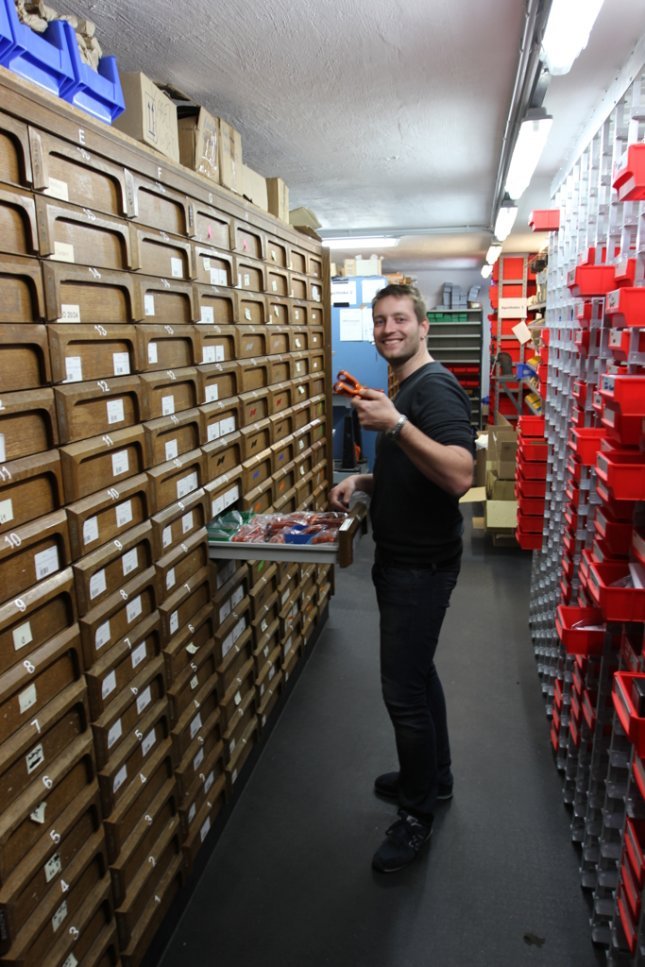
Jan-Felix konfektioniert die Rahmenteile für das jeweilige Rahmenmodell
Fazit
Die Arbeitsschritte und den enormen Zeitaufwand bei der Produktion eines ION 16 Rahmen zu sehen ist extrem beeindruckend. Durch den Besuch bei Nicolai habe ich gelernt ein Nicolai Mountainbike nicht als selbstverständlich anzusehen, sondern als das, was es ist: Ein handgemachtes Kunstwerk und präziser Maschinenbau. Für mich ist klar, dass ich ein Nicolai ION 16 brauche. Da ich bei einer Körpergröße von 2,02 m einen super großen Rahmen brauche, ist dies jedoch eine Spezial-Größe. Doch wenn nicht bei Nicolai, wo sonst könnte ich mir einen Rahmen perfekt für meine Größe machen lassen? Die Entstehung eines solchen Tailor Made-Rahmens werde ich euch in meinem nächsten Bericht vorstellen.