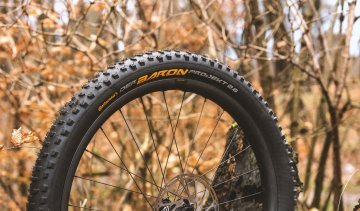
Im Test: Continental Der Baron Projekt 2.6
Der Baron Projekt wurde von Continental neu aufgelegt und verbessert. Mit 2,6" ist er nochmal breiter als sein Vorgänger.
Wir haben uns die Produktion von Continental angeschaut. In Korbach werden alle High Performance Reifen mit der Black Chili Mischung hergestellt.
Continental blickt auf eine lange Tradition als Reifenhersteller zurück, schließlich werden bereits seit 1871 Reifen für die unterschiedlichsten Gefährte produziert. Wir waren zu Gast im beschaulichen Korbach, wo in einem 3000 Mann starken Werk die High-Performance-Fahrradreifen „Made in Germany“ mit der bekannten Black Chili Mischung produziert werden. Anlass unseres Besuchs war die Produktion des nagelneuen „ Der Baron Projekt 2.6“.
Ausgangspunkt unserer Führung war nach einem netten Empfang in einem prunkvollen Gebäude das Produktmanagement, wo die klugen Köpfe hinter den Reifen sitzen. Dort haben uns Ben und Alex empfangen, die uns den ganzen Tag begleiten sollten. Sie haben uns fast jeden Wunsch erfüllt und uns alles gezeigt, was wir sehen wollten, an dieser Stelle schon mal ein dickes Dankeschön an die zwei. Ben ist der Kopf hinter allen Rennrad- und Trekking-Reifen, wohingegen Alex der Experte für den Bereich Mountainbike ist. Aufgrund der langen Tradition von Continental in der Herstellung von Auto- und LKW-Reifen, können die Projektmanager auf einen riesigen Erfahrungsfundus an unterschiedlichsten Gummimischungen zurückgreifen und sich die Mischungen nach ihren Vorstellungen zusammenstellen.
Nach dem netten Empfang und einem kleinen historischen Exkurs in die Firmengeschichte, gingen wir nun voller Vorfreude in die Produktion. Schließlich waren wir gespannt darauf zu sehen, wie die Reifen Schritt für Schritt entstehen. Los ging es im Kalander Saal - ein gut gehüteter Raum zu dem nur wenige Continental Mitarbeiter Zutritt haben - hier wird das Gummi mit einem Stoffgewebe verbunden. Dabei wird immer eine Lage Gummi, Stoff und dann wieder Gummi zusammengefügt. Das Verbinden der einzelnen Karkassenlagen nennt man „Kalandrieren“.
Die Stofflage zwischen den Gummischichten, sowie die Dicke des Gummis, können je nach Reifenmodell variieren. Der Stoff unterscheidet sich dabei in der Dicke der Fäden. Trotz des dreischichtigen Aufbaus ist es möglich, eine Materialdicke von unter 0,5 mm zu erreichen. Dieser Verbundstoff bildet die Karkasse des Reifens.
Die Stoffbahn der Reifenkarkasse muss noch zugeschnitten werden.
Die Lauffläche des Barons und aller in Korbach gefertigten Reifen ist aus der bekannten Black Chili Mischung. Zwar trägt die Mischung stets den Namen Black Chili, doch sie wird immer speziell für den individuellen Einsatzbereich des Reifens angepasst.
Die Rohmasse der BlackChili Lauffläche wird dabei in einen Extruder geführt, dort wird sie zerkleinert und so weit erhitzt, dass das Material anfängt zu fließen und formbar wird. In die endgültige Form wird es gebracht, indem das Gummi durch eine Matrize gepresst wird. Durch diesen Vorgang werden Materialmenge und -form festgelegt.
Der Zusammenbau des Reifens erfolgt immer nach dem gleichen Schema und erfordert unerwartet viel Handarbeit. Alle Reifenkomponenten werden in festgelegter Reihenfolge auf eine spezielle Expander-Trommel gelegt, diese kann sich drehen und ihren Durchmesser vergrößern.
Zuerst wird die Karkasse auf die Trommel aufgelegt, bevor die Reifenkerne oder Wülste und das Apex-Material hinzugefügt werden. Nun wird das an der Seite überstehende Karkassenmaterial über die Reifenwülste in Richtung Mitte geklappt. Zum Schluss werden die Decals und die Lauffläche hinzugelegt. Bei all diesen Schritten wird kein Kleber verwendet, da die Materialien nur aufgrund des Anpressdrucks schon aneinander haften. Erst im nächsten Schritt, dem Backen, werden die einzelnen Schichten miteinander verbunden und der Reifen bekommt sein individuelles Profil.
Der sogenannte „Apex-Layer“ ist ein Kautschuk Profil, dass in die Seitenwand eingearbeitet wird. Es stabilisiert großvolumige Reifen während Kurvenfahrten und verhindert somit „Tire Burping“, also den Luftverlust, weil der Reifen kurz von der Felge abspringt.
Apex gibt dem Reifen einen besseren Seitenhalt in Kurven.
Das Vulkanisieren ist wohl einer der wichtigsten Schritte in der Produktion. Ohne dieses dem Backen recht ähnliches Verfahren hätte der Reifen keine Form, kein Profil und würde sich wahrscheinlich unter Belastung in seine Einzelteile auflösen. Außerdem ist das Material erst nach dem Vulkanisationsprozess elastisch, vorher lässt sich das Material plastisch verformen.
Vulkanisiert wird der Reifen in einer Art Presse. Der Grünling wird um den runden Mittelteil der Presse gelegt. In diesem Mittelteil befindet sich ein Blasebalg, der den Reifen ausbeult und ihm seine Form verleiht. Im äußeren Ring der Presse werden die Formen für die verschiedenen Profile eingelegt. So drückt der Blasebalg in der Mitte das Material der noch flachen Lauffläche in die Profilform. Bei einer Temperatur von ca. 170 °C wird der Baron unter 16 bar Druck für 280 Sekunden gebacken, bevor er endgültig bereit für den Trail ist. Die Backtemperaturen, Drücke und Zeiten sind natürlich je nach Reifen unterschiedlich.
Der Baron Rohreifen vor dem Vulkanisieren.
Beim Vulkanisieren wird das Profil ausgeformt.
Der Tag bei Continental war beeindruckend. Für mich war es überraschend zu sehen, wie viel Handarbeit in einem technisch so hochentwickelten Produkt steckt. Continental hat alle Bereiche der Reifenproduktion in eigener Hand und kann so die Eigenschaften der Reifen bzw. der Gummimischungen präzise auf die Anforderungen der jeweiligen Einsatzgebiete anpassen. Ich werde den Continental Baron 2.6 diese Saison auf jeden Fall mal ausprobieren! Mein Kollege Stefan ist ihn bereits Probe gefahren und ist überzeugt vom neuen Gripwunder aus Korbach.
Das könnte Dich auch interessieren
Das Citybike zum urbanen Pendeln - und für alles, was Du draus machst! Lass das Auto stehen und erlebe mehr Freiheit mit dem Vortrieb Modell 1.2.
Braucht ein Kinderrad Beleuchtung? Ist ein Kettenschutz vorgeschrieben? Und besteht eine Helmpflicht für Kinder? Wir helfen Dir und Deinem Kind weiter.